One question we’re frequently asked is, “I have this challenge and want to solve it this way. Can you make this thing I have in mind?”
Sometimes “the thing” is similar to something we already make, such as a Pull Roll we created to help a manufacturer pull different thicknesses of cardboard through the line.
Other times, “the thing” is something that doesn’t exist at all – except maybe as an idea sketched out on a napkin. (Not that we get drawings on napkins, but you get our drift.)
Case in point, a few years ago, an OEM needed to create a check valve for waste water treatment facilities. This check valve, which would be used to prevent back flow into a pipe (as well as continuous running of the pump), needed a weighted ball that met specific requirements in order for the project to work:
- It had to be made of urethane – and be perfectly round.
- It had to house an internal steel ball or core – which had to be perfectly centered inside the urethane.
- It had to weigh a specific amount – and not an ounce more.
- It had to sit perfectly atop a seal inside the check valve.
(Notice how many times that word “perfectly” was used? Yes, we did too!)
Challenge: Centering the steel ball
Making a custom mold for a urethane sphere or ball isn’t difficult, as far as molds go. The challenge with this particular part, however, was creating the tooling — and a process — that would allow us to keep the steel ball perfectly centered while the urethane was poured and cured.
If the steel ball weren’t perfectly centered, the “heavy” side of the ball would keep landing in the same spot — thus wearing the ball in one particular spot prematurely and significantly shortening the useful life of the ball.
It would also create the potential for waste water to back flow into the pipe and the pump then running continuously (and thus equipment failure).
After a number of test runs, we met the customer’s main requirement for ensuring the inner core was perfectly centered – as you can see in the following photo.
In addition, we had to experiment with urethane formulations to ensure the urethane cover could withstand continuous “seating” on the pipe opening — as well as the harsh conditions of the wastewater.
Continuous improvement = better performance and longevity
Part of our job is to help our customers save money while improving their part performance.
One way we do this is through continual engineering improvements. Based on feedback from our craftsmen, for example, and using Autodesk Inventor®, we’ve suggested and implemented dozens of small modifications to improve the performance of the check valve ball – without the OEM having to pay more per part.
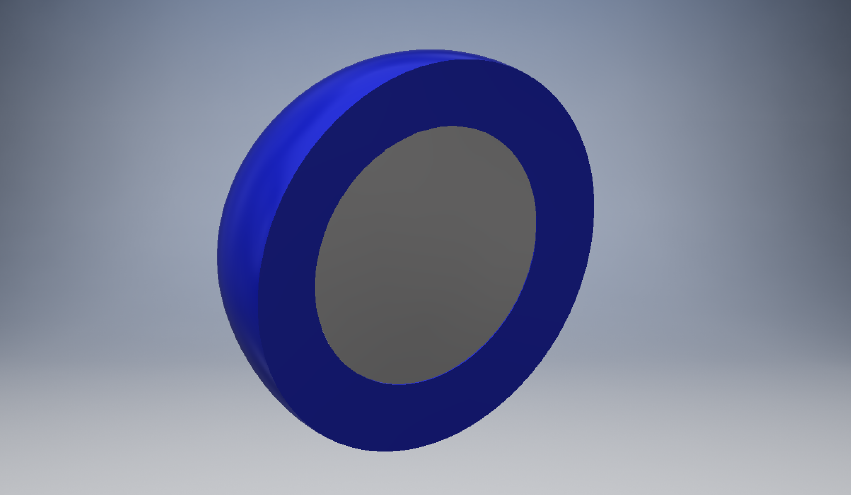
And, we continue to tweak the urethane formulation to improve material longevity without adding to the weight or size of the ball.
The result is a part that meets our customer’s exacting requirements and improves the uptime of waste water treatment plants — while reducing the time needed to switch out worn check valves.
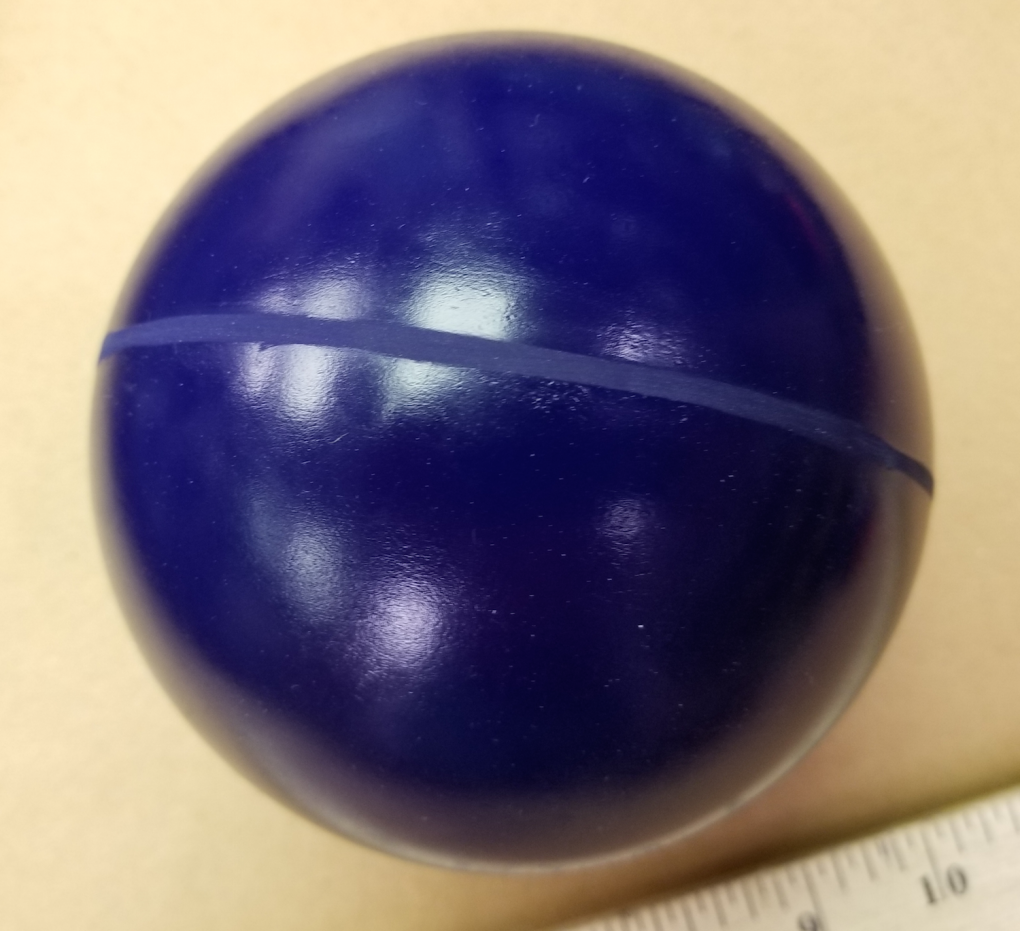
If you’ve got a “thing” you need made, but you’re not sure if it can be done, give us a shout. We have over 50 people working here, and by putting our heads together, we can pretty much solve just about any challenge you give us.